
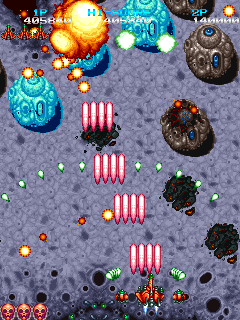
Your firm failed to establish a written distribution procedure to include a system by which each lot of drug product can be readily determined to facilitate its recall if necessary (21 CFR 211.150(b)). In your response to this letter, provide your complaint handling procedure, including cataloguing, tracking, and investigating complaints.Ĥ. However, this procedure is inadequate because it lacks adequate provisions to investigate the complaints you receive. In response to our inspection, you drafted and submitted a complaint handling procedure. Your firm did not maintain a record of the complaint or investigate it to determine the cause of the labeling mix-up. The product received was actually Phenobarbital Tablets USP (30 mg, 1000 count.) You sold this drug product to both human and animal clinics. You received a complaint regarding a bottle labeled as Phenobarbital Tablets USP (15 mg, 1000 count), lot 70952A. Your firm lacked an adequate procedure for handling complaints. Your firm failed to establish and follow adequate written procedures describing the handling of all written and oral complaints regarding a drug product (21 CFR 211.198(a). In your response to this letter, provide your plan, including written procedures, to ensure compliance with CGMP for all drug repackaging activities in which you engage.ģ. You did not address this observation in your response. In the affidavit collected during the inspection, you stated, “I have no records to show the repackaging operation.” You incorrectly labeled a container filled with Phenobarbital tablets 30 mg as Phenobarbital tablets, USP 15 mg (schedule IV) lot 70952A. Your firm performs repackaging and labeling operations but did not have written procedures governing the application of packaging and labeling materials to your drug products. Your firm failed to establish and follow written procedures to assure that correct labels and packaging materials are used for drug products (21 CFR 211.130). In addition, specify which operations your firm has ceased to perform and the dates on which such operations were halted.Ģ. In your response to this letter, provide your procedure detailing the responsibilities of the quality control unit, and outline your repackaging operations with their corresponding procedures. Truxton Inc., in the future.” We are unclear as to what specific items you referred to in your response. You stated that “some items were not addressed, as they should not have been done and will not be done by C.O. Your firm failed to establish a quality control unit for your drug repackaging operation and you lacked written procedures for production or quality unit responsibilities. Your firm failed to establish a quality control unit with the responsibility and authority to approve or reject all components, drug product containers, closures, in-process materials, packaging materials, labeling, and drug products (21 CFR 211.22(a)).
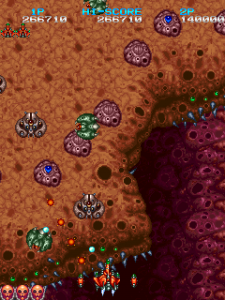
We reviewed your June 14, 2017, response in detail.ĭuring our inspection, our investigator observed specific violations including, but not limited to, the following.ġ. By introducing adulterated and misbranded drugs into interstate commerce you are in violation of section 301(a) of the FD&C Act, 21 U.S.C. In addition, your firm mislabeled drug products, causing them to be misbranded under section 502(b)(2) and 502 (e)(1)(A)(ii) of the FD&C Act, 21 U.S.C. See 21 CFR, parts 210 and 211.īecause your methods, facilities or controls for manufacturing, processing, packing, or holding do not conform to CGMP, your drug products are adulterated within the meaning of section 501(a)(2)(B) of the Federal Food, Drug, and Cosmetic Act (FD&C Act), 21 U.S.C. This warning letter summarizes significant violations of current good manufacturing practices (CGMP) regulations for finished pharmaceuticals. (“Truxton”), at 136 Harding Avenue, Bellmawr, New Jersey (FEI 2220338), from April 17 to June 1, 2017. Food and Drug Administration (FDA) inspected your drug manufacturing facility, C.O.
